Dieffenbacher Emission Control Systems
Dieffenbacher’s emission control solutions include emission measurements and dryer and press emission control systems. Emission measurements help plant operators understand which emissions are present and determine the type and amount of emissions. For example, using state-of-the-art methods, uncomplicated in-house emission measurements can be taken on stacks downstream of the dryer or the press exhaust system. This includes measuring parameters such as total organic carbon (TOC) and many different substances such as water, carbon dioxide, carbon monoxide, nitrous oxide, methane, ethane, propane, formaldehyde, methanol and other gases. Dust in the exhaust gas can also be measured using additional equipment. Subsequent correlation analyses of production parameters and emissions provide a better understanding of plant emissions.
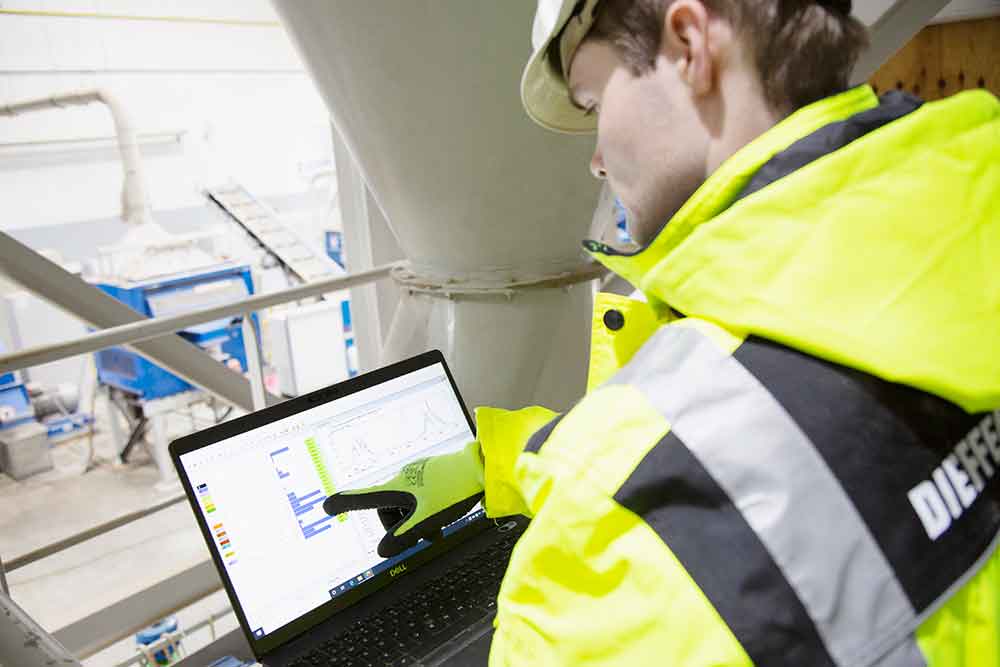
The Dryer Emission Control System cleans dryer exhaust gases using an inline scrubber in compliance with local environmental standards. The main components are the unique inline scrubber and water treatment and distribution systems. The inline scrubber efficiently separates dust particles from the gas stream. Optional auxiliary equipment captures water-soluble VOCs, notably formaldehyde. The Dryer Emission Control System is applicable for horizontal and vertical operation and costs less than an electrostatic filter. It also impresses with its low freshwater demand, reliable design for high uptime and small space requirements.
The Press Emission Control System cleans exhaust gases from the press through a washing process. Dust and condensable fractions of exhaust gases are bound to fine water droplets. These solid and liquid parts are separated in the inline scrubber. Pre-Absorber units can be supplied to reduce VOC emissions (volatile organic compounds), particularly formaldehyde. As a fluid-optimized system, the Press Emission Control System is highly energy-efficient. Like the Dryer Emission Control System, it is characterized by low freshwater demand and small space requirements.
Latest News
Sweet Sixteen
Article by Rich Donnell, Editor-in-Chief, Panel World May 2019 – No, the headline doesn’t refer to the NCAA basketball tournament and the prestige of reaching the tournament’s Sweet Sixteen finalists. Rather it tells the number of Ligna shows in Hannover, Germany I will have attended, if indeed I make the upcoming…
MSU Building Using CLT, Glulam Products
MSU Building Using CLT, Glulam Products The Michigan State University STEM Teaching and Learning Facility will be the first in Michigan to use mass timber wood products, rather than concrete and/or steel, for its load-bearing structure. The $100 million...
Freres Lumber Named One Of 2019’s Most Innovative Companies
Freres Lumber Named One Of 2019’s Most Innovative Companies Freres Lumber Company has been named to Fast Company’s annual list of the World’s Most Innovative Companies for 2019, ranking as the fifth on the Most Innovative Company List in the Urban...
CalAg Rice Straw MDF Plant
CalAg Rice Straw MDF Plant Here’s how the new CalPlant I (CalAg) rice straw based MDF plant in Willows, California looked as of February 5, 2019, compliments of CEO Jerry Uhland. The $315 million facility is expected to start up in the third quarter and will...
After All These Years GP Still Knows Plywood
Article by Rich Donnell, Editor-in-Chief, Panel World March 2019 – Our friends Dick Baldwin and Rich Baldwin write about the North America softwood plywood industry in this issue. They note that about 28 plywood mills disappeared since pre-recession or…
Find Us On Social
Newsletter
The monthly Panel World Industry Newsletter reaches over 3,000 who represent primary panel production operations.
Subscribe/Renew
Panel World is delivered six times per year to North American and international professionals, who represent primary panel production operations. Subscriptions are FREE to qualified individuals.
Advertise
Complete the online form so we can direct you to the appropriate Sales Representative. Contact us today!