Dieffenbacher Emission Control Systems
Dieffenbacher’s emission control solutions include emission measurements and dryer and press emission control systems. Emission measurements help plant operators understand which emissions are present and determine the type and amount of emissions. For example, using state-of-the-art methods, uncomplicated in-house emission measurements can be taken on stacks downstream of the dryer or the press exhaust system. This includes measuring parameters such as total organic carbon (TOC) and many different substances such as water, carbon dioxide, carbon monoxide, nitrous oxide, methane, ethane, propane, formaldehyde, methanol and other gases. Dust in the exhaust gas can also be measured using additional equipment. Subsequent correlation analyses of production parameters and emissions provide a better understanding of plant emissions.
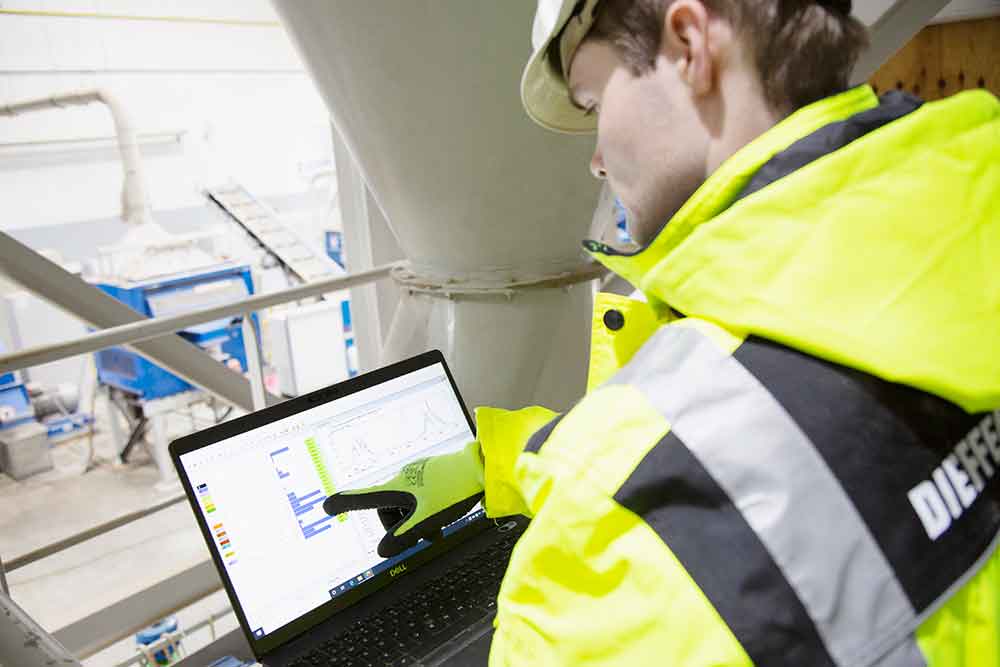
The Dryer Emission Control System cleans dryer exhaust gases using an inline scrubber in compliance with local environmental standards. The main components are the unique inline scrubber and water treatment and distribution systems. The inline scrubber efficiently separates dust particles from the gas stream. Optional auxiliary equipment captures water-soluble VOCs, notably formaldehyde. The Dryer Emission Control System is applicable for horizontal and vertical operation and costs less than an electrostatic filter. It also impresses with its low freshwater demand, reliable design for high uptime and small space requirements.
The Press Emission Control System cleans exhaust gases from the press through a washing process. Dust and condensable fractions of exhaust gases are bound to fine water droplets. These solid and liquid parts are separated in the inline scrubber. Pre-Absorber units can be supplied to reduce VOC emissions (volatile organic compounds), particularly formaldehyde. As a fluid-optimized system, the Press Emission Control System is highly energy-efficient. Like the Dryer Emission Control System, it is characterized by low freshwater demand and small space requirements.
Latest News
Remodelers Report Material Shortages
Though markets have cooled a bit going into the fourth quarter 2020, remodelers reported extensive materials shortages during third quarter 2020, according to a…
Ligna Changes 2021 Show Dates
Organziers of the Ligna show—Deutsche Messe and VDMA—announced that the large woodworking machinery event next year is rescheduled from May to September 27 to October 1, 2021. The announcement comes in view of ongoing developments and…
Sometimes The Paths Come Full Circle
Article by Rich Donnell, Editor-in-Chief, Panel World November 2020 – We know that people’s paths may cross; the same can be said of articles in Panel World. You’ve probably noticed that the cover article for this issue is on the Winston Plywood & Veneer operation in Louisville, Miss…
Survey Cites Biggest Wood Flooring Threats
A wide ranging survey recently undertaken by the National Wood Flooring Assn. looked at the impact of the viral pandemic on the flooring industry and the…
Egger Starts Up In North Carolina
Egger completed its first raw particleboard production line at its new manufacturing facility in Lexington, NC. Employees watched as the first panel underwent the final stages of production, transforming raw wood chips into a finished…
Find Us On Social
Newsletter
The monthly Panel World Industry Newsletter reaches over 3,000 who represent primary panel production operations.
Subscribe/Renew
Panel World is delivered six times per year to North American and international professionals, who represent primary panel production operations. Subscriptions are FREE to qualified individuals.
Advertise
Complete the online form so we can direct you to the appropriate Sales Representative. Contact us today!